Progressive Design-Build
Intro to Design-Build
When operating under traditional project delivery models such as Design-Bid-Build, the owner holds separate contracts with the design team and the construction team. The lack of contract-forced communication between the design and build teams forces the owner to serve as an in-between and also leads to rework as the two teams fail to properly coordinate their efforts.
Design-Build is gaining popularity as an alternative delivery method, with nearly half of all construction projects now using it. One of the main reasons for this is that it produces results: Design-Build (and by extension, Progressive Design-Build) performs far better when it comes to cost and quality of the project delivered.
While not strictly a Lean practice, Design-Build does allow for more collaboration for the two teams and lends itself to the possibility of implementing Lean methods. This makes it a great starting point for any team looking to dip their toes into Lean methodology.
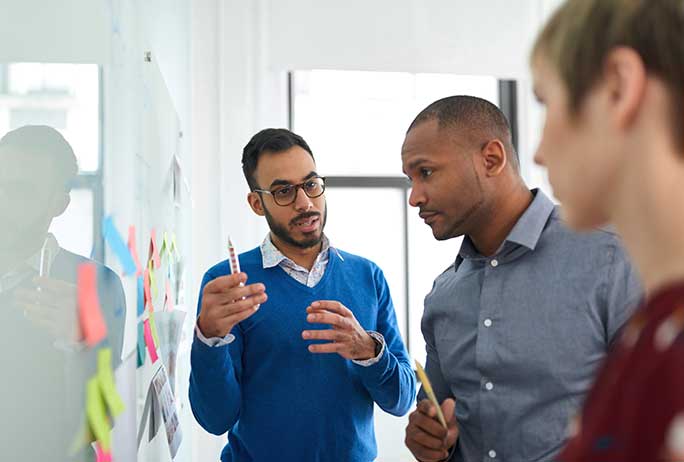
Design-Build Contracts
Design-Build contracts are characterized by the construction and design team – along with any trades needed – working from the same contract which is co-signed by the owner. This contract forces the design and build teams to work together from the start of the project through to its completion.
Intro to Progressive Design-Build
Just because you’re working from a Design-Build contract structure rather than using Integrated Project Delivery doesn’t mean you can’t be Lean and implement Lean structures.
What is Progressive Design-Build?
In general, Design-Build is a more integrated form of project delivery than the typical Design-Bid-Build structure, making Design-Build a huge improvement for delivering value. However, by adhering to more Lean principles, Design-Build construction projects can deliver even more value.
What's The Goal?
The goal of Progressive Design-Build is to use Lean Construction principles while operating from a Design-Build contract.
Design-Build Projects
Check out this video from LCI member and host of The EBFC Postcast<, Felipe Engineer-Manriquez. Here he interviews Tania Gharechedaghy about her experience as the Owner’s Responsible-in-Charge Project Manager leading a $1B Design-Build Project.
Features of Progressive Design-Build
- The owner and design-builder (the representative of the design & building teams, which is most often the design firm in a Design-Build contract) remain in constant contact throughout the process to ensure the project is delivered on budget and meets the owner’s expectations. This provides the owner with more control and oversight of the project than they’d normally have in a Design-Build project.
- The design-builder is selected based on qualifications, not bid price, ensuring the highest possible value is delivered.
- The project is completed in two separate and distinct phases, with the first phase covering pre-construction and the creation of designs, while the second phase covers the completion of the designs and construction of the project.
Phase 1
During this phase while using a Progressive Design-Build approach, the design-builder begins the process of designing the project, remaining in contact with the owner as budgetary needs change and ideas are exchanged.
Once the design has reached a satisfactory point that meets the owner’s expectations, a formal commercial project proposal can be written. This generally occurs when the design is at least halfway complete.
Phase 2
In some rare scenarios, the Phase 2 work can begin while Phase 1 work is already being completed – without a formal commercial contract yet completed – for the purpose of expedition.
During this phase, the design and build teams complete their work based on the terms of the commercial contract. Should talks stall out regarding an agreement on commercial terms, the owner has the option to move the project to another contract strategy.
Tips for Being Lean in Design-Build
Design-Build is a project delivery method that provides many more opportunities to be Lean than traditional Design-Bid-Build methods. Here are some other ways you can integrate Lean concepts into your Design-Build project.
- In the spirit of Conditions of Satisfaction, let the project’s objectives drive the process and ensure that every step in the process is working to achieve a goal or set of goals. The owner should set goals that are reasonable and attainable, with clear performance-based incentives that promote innovation.
- Owners are expected to develop realistic budgets for projects while communicating clearly about their budgetary restrictions.
- All contracted parties should work to identify project risks and agree to work collaboratively to ensure these risks are addressed in advance.
- All members of the team using Progressive Design-Build must be aligned that the level of success the project can achieve is dependent upon the parties’ willingness to collaborate and problem solve in constructive ways.
Lean Tools to Use in Design-Build
Many Lean tools support Design-Build projects (LCI partners with the DBIA on many Lean initiatives). Below are some, but not all, Lean tools and approaches that you can implement into your Design-Build projects.
Daily Huddles & Big Room
Daily Huddles are regularly-scheduled daily meetings between all relevant members of a project team in which the team discusses project updates and what needs to be accomplished before the next meeting. Big Room is another type of regular meeting between key stakeholders but the topics discussed are more big picture, looking at the project scope as a whole.
Last Planner System®
The Last Planner System can enhance process and flow in Design-Build construction projects by promoting productive conversations between team members on a regular basis so problems can be identified and solved before they disrupt the work being completed.
Target Value Delivery
Target Value Delivery is a project delivery method that aims to reduce waste by ensuring the needs of the project are consistently considered and satisfied throughout the process and by dividing the project into distinct phases to follow.
Gemba Walks
Gemba walks are useful for seeing how the processes are actually being completed on-site, allowing the design-builder to identify problems in the workflow. Through this process, the team can eliminate waste and increase the likelihood that the project is delivered on time.
5S
5S is a mindset for organization on the job site. The goal of 5S is to ensure that equipment, information, and materials are provided to the proper people at the proper time, saving time for all members of the project team while also making the workplace safer.
Value Stream Mapping
Value Stream Mapping is a process of mapping out the workflow processes to determine what steps are adding value to the final product and which steps are wasteful and can be eliminated.
5 Why
5 Why is a method for root cause analysis that guides team members towards the cause of a problem occurring on-site so that the team can collectively devise an effective solution.
Learning Progressive Design-Build
Lean Construction Institute is committed to transforming the design and construction industry by providing educational resources, conducting surveys and research, and facilitating local and national Lean events. It is only through the power of the LCI Corporate Members that LCI is able to offer the supplementary resources below to help you better understand Progressive Design-Build.
Lean Assessments
How strong is your Lean knowledge? Take a Lean assessment to determine your current state so you have a baseline for improvement. Lean assessments are available for individuals, teams, and organizations alike. Whether you’re new to Lean or are an experienced Lean practitioner, Lean assessments are a great way to get started at LCI!
TAKE ASSESSMENTMore Lean Topics
From 5s to IPD, explore popular Lean design and construction topics below.