What is Lean Thinking?
An Introduction to Lean Thinking
What is Lean? First and foremost, it’s important to think of Lean as a mindset, a way of thinking, rather than a technique. Lean requires buy-in from a team that is focused on continuously improving working processes to seek the best possible outcomes. Ultimately, Lean is a shift in how a team works together.
The goal of Lean is to generate more value for customers and stakeholders. Lean improvement methodologies achieve more value by the removal of waste in processes. A successful Lean enterprise accomplishes all of this by opening up the lines of communication between parties and by instilling trust among teams and team members.
Lean Defined:
A Way of Thinking, Process & Culture
Lean is a culture of respect and continuous improvement aimed at creating more value for the customer while identifying and eliminating waste. Across the construction and design industry, Lean as a process, a culture and a way of thinking proves to be effective in doing just that.
Who Uses Lean?
Lean can be applied to many different industries. Today, it’s primarily used in…
- Education
- Healthcare
- Government
- Construction
- Engineering & Architecture
- Manufacturing & Production
- High Tech Software Development
- Project Management
- Service Industries
The Purpose of Lean
- Generate value for all stakeholders
- Produce projects/products on-time and on-budget
- Eliminate waste and increase productivity
- Create a safer, more collaborative work environment
A Brief History
Lean technically dates back to as early as 15th century Italy, but the modern Lean principles were developed by Toyota following World War II. Toyota’s founders built upon many of the systems that made Henry Ford so successful in mass production of vehicles.
In true Lean fashion, Toyota sought continuous improvement and turned Ford’s weaknesses – overproduction and a lack of customization – into strengths. This is how the Toyota Production System was born.
Today, Lean methodologies are utilized by several of the world’s most successful companies including Nike, Intel, John Deere, and Caterpillar. LCI provides learning opportunities for owners, general contractors, construction project managers, designers and tradesmen to learn Lean processes in the construction and design industry.
Toyota and Lean
Toyota made a number of improvements, including the discovery that it could use a pull system to ensure it was only using materials when they were really needed. Toyota operated based on its 14 principles of Lean which still guide the company today.
Lean Thinking
For Process Improvement
Lean thinking is a shift towards a mindset of continuous process improvement. This concept is often referred to as Lean process improvement: a continuing evolution of processes leads to increasing generation of value.
Lean thinking also involves the implementation of ongoing line of communication from within specific teams and without; those in charge of each team must communicate with all others on their team and also with other teams involved on the project.
While Lean has to be led and supported from the top, it’s crucial that the implementation happens at the most basic level of the operation. Those who are on the ground delivering the value are the most critical cog in the machine with regards to delivering the value efficiently while eliminating waste.
Lean Principles
Many in the Lean industry believe that there are five main principles of Lean methods. The five commonly-referenced principles are:
- Define Value
- Identify the Value Stream
- Focus on Flow
- Establish Pull
- Pursue Perfection
In general, the Lean Construction Institute agrees that these five principles are key for any Lean organization. However, LCI prefers to refer to the six tenets of the Lean Construction Institute as we believe these more fully encompass Lean across the AEC industry.
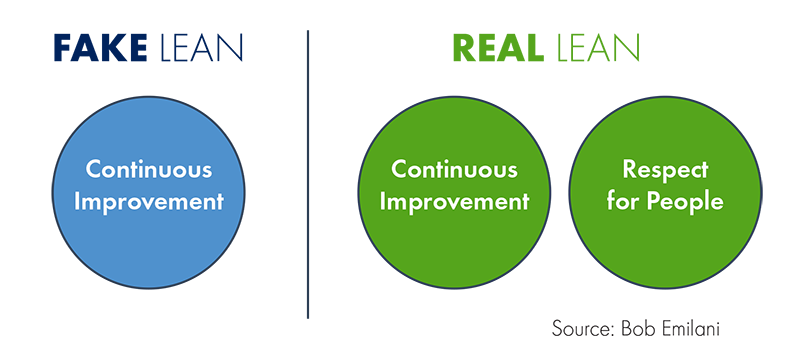
1. Respect for People
We start with Respect for People because it is paramount that any Lean production process features a healthy amount of respect, both for the customers and for fellow team members. A Lean enterprise without a foundation of trust is a failing one from the start, even if that organization adheres to the five core principles listed above.
Lean Principles
2. Optimize the Whole
In the design and construction industry, many organizations become concerned only with their individual part of a project. They seek to get in, do their part, and get out. Any successful Lean practice will ask: how can your process benefit not only your work, but also the work of those who came before you and those who come after you on that project?
A rising tide lifts all boats, and more can be accomplished together if everyone seeks to produce the best overall outcome rather than simply the best outcome for their individual piece of the puzzle. In fact, many Lean contracts include clauses to split profits across all facilitators of a project which is delivered (using lean tools) on-time and on-budget.
3. Removal of Waste
The Lean Construction Institute recognizes eight different types of waste that can be found in modern production processes. A shift to a Lean mindset means getting into the habit of looking for and reducing waste in current processes.
4. Focus on Process & Flow
Flow is the notion that every team involved in a project can get their work done smoothly and unimpeded by the work of others on the project. Reducing wait times and removing constraints is a major component to Lean. Once teams learn to communicate with and trust in each other, they’ll find that their flow is greatly enhanced, thus improving productivity.
5. Generation of Value
Value can be thought of as the opposite of waste. Something that is value inherently cannot be wasteful. It’s critical to identify the value proposition in the project you’re completing and then to tailor your processes to generate as much value as possible.
6. Continuous Improvement
Implementing Lean methods into a process means continuously improving processes to improve flow, generate more value, and eliminate waste. Lean methods often use what are called PDCA processes: Plan, Do, Check, Adjust. Plan the process that you want to utilize, implement the process, check to see where you can improve upon that process, and take action accordingly to optimize outcomes.
Lean Practices
There are many practices Lean experts use to maintain flow in their processes. Some effective Lean practices include:
- Kanban – “Kanban” is a Japanese term meaning “a signboard.” A communication tool used in JIT production systems. The signal tells workers to pull parts or refill material to a certain quantity used in production.
- Last Planner System® – LCI helps companies establish pull in their Lean methodologies through our Last Planner System.
- Gemba Walks – Gemba walks are an effective way to see how work is currently being performed and to determine potential ways to improve processes.
- A3 – A one-page report prepared on a single 11 x 17 sheet of paper that adheres to the discipline of PDCA thinking as applied to collaborative problem solving, strategy development or reporting. The A3 includes the background, problem statement, analysis, proposed actions, and the expected results.
- 5S – A disciplined approach to maintaining order in the workplace, using visual controls, to eliminate waste. The 5S words are Sort, Set in Order, Shine/Sweep, Standardize and Self-Discipline/Sustain.
Lean Tools
Lean tools help people to implement Lean practices in their processes. Some Lean tools include:
Learning Lean
The Lean Construction Institute is committed to transforming the design and construction industry by providing educational resources, conducting surveys and research, and facilitating local and national Lean events. It is only through the power of the LCI Corporate Members that LCI is able to offer the supplementary resources below.
Lean Assessments
How strong is your Lean knowledge? Take a Lean assessment to determine your current state so you have a baseline for improvement. Lean assessments are available for individuals, teams, and organizations alike. Whether you’re new to Lean or are an experienced Lean practitioner, Lean assessments are a great way to get started at LCI!
TAKE ASSESSMENTLean Assessments
How strong is your Lean knowledge? Take a Lean assessment to determine your current state so you have a baseline for improvement. Lean assessments are available for individuals, teams, and organizations alike. Whether you’re new to Lean or are an experienced Lean practitioner, Lean assessments are a great way to get started at LCI!
TAKE ASSESSMENTMore Lean Topics
From 5s to IPD, explore more popular Lean design and construction topics below.