Lean Industrialized Construction
Introduction to Industrialized Construction
This Lean Topic article was written by the LCI team in collaboration with Nick Masci, Melissa McEwen, and Sally Mizell of Haley & Aldrich’s Lean consulting team.
As we know, Lean thinking has its roots in the manufacturing industry, becoming popularized by the Toyota Production System before making its way to the built environment. Today, Lean methodologies are used across the design and construction industry, and we’re constantly adapting and innovating to create new, more effective methods that work for construction.
But we can still learn so much from the way manufacturing systems run.
Enter industrialized construction, an approach that draws on effective manufacturing principles to make the production of buildings more effective for consumers, designers, and builders.
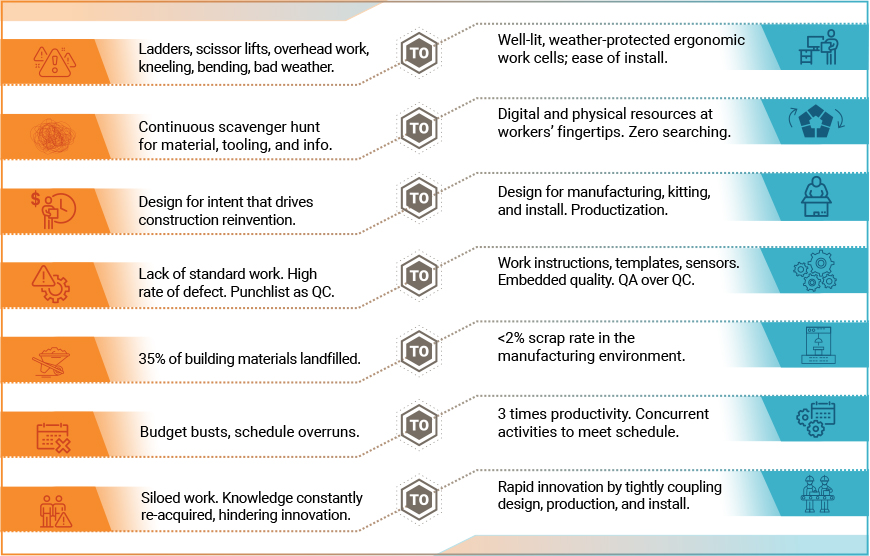
What Is Industrialized Construction?
Industrialized construction applies manufacturing techniques to the built environment. It borrows from the actual product development, engineering, production, and materials management workflows of manufacturing and the aspects of the culture that drive success.
The Industrialized Construction Movement
The industrialized construction movement aims to achieve three main big-picture ends: higher quality (better), shorter delivery time (faster), and reduced cost (cheaper), in that order. Underlying these ends is the overarching drive to improve things for our customers, our workers, and our communities.
Industrialized construction has far-reaching potential. It can transform our approach to design, materials and products, and supply chain partnerships. Lean principles and systems, if adopted holistically, are transformative. Industrialized construction offers a framework for the fundamental shifts needed across the construction industry — moving from a disconnected design process to fully digital designs based on project data and from buying one-off projects to buying sustainable, productized buildings.
Holistic Benefits of Industrialized Construction
- Better business decisions derived from the systematic use of data
- Increased decarbonization and support for ESG initiatives
- Improved employee problem-solving skills and greater empowerment
- Fewer injuries and body aches/better quality of life for workers
- More productive partnerships
Foundations of Industrialized Construction
From Respect for People and continuous improvement to prefabrication, modularization, and kitting, the foundations of industrialized construction aim to improve all aspects of a project.
Respect for People
It is well documented that more efficient processes, stronger lines of communication, access to the right information and resources, and collaborative problem-solving lead to more engaged and happier workers.
Industrialized construction draws on a Lean mindset to meld the prefab process and worker-centric manufacturing with design, logistics, and installation — ultimately striving to create a self-sufficient operation where everyone in the system has real-time access to the information and resources they need to do their work. Industrialized construction fosters better engagement and job satisfaction.
Furthermore, by creating a system that seeks to optimize ergonomics and bring the work to the worker, industrialized construction can help make jobs more accessible. For instance, people with knee or back issues can’t do labor-intensive work on a construction site, but in an industrialized construction setting, they can work at a station, which eliminates the harsh physical toll.
As they foster worker engagement, industrialized construction concepts need worker engagement to take hold. Real integration is only possible by engaging people across the value chain — owners, trades, superintendents, engineers, product suppliers, plant managers, and software engineers — to help them see, understand, and act together.
Industrialized Construction Is Built on Respect for People
- Safer jobs with opportunities to learn new economy skills
- Enhanced teamwork
- Multifunctional workers
- Decentralized responsibility
- Increased motivation
- Better capture of employee ideas
Continuous Improvement
Continuous improvement is the concept that major changes will manifest over time through the accumulation of many small improvements. In a factory or fab shop, where you have a stable workforce, it becomes easier for those benefits to accumulate and for people to transmit knowledge between projects and teams.
Prefabrication, Modularization, and Kitting
While not everyone is familiar with the idea of industrialized construction, many are familiar with modular construction and prefabrication — “prefab” for short — which are key facets of the movement.
In industrialized construction, the goal is to identify the most efficient ways to deliver the materials and components that meet the customer’s program needs (value) with the right level of resources (materials, labor, time, dollars). Industrialized construction calls for identifying products — even for types of work traditionally thought of as services (e.g., skilled craftwork), not products — and components that can be prefabbed, pre-assembled, and/or kitted to improve the flow, speed, and cost of installation in the field.
Benefits of Industrialized Construction
As mentioned above, industrialized construction aims to achieve three overarching ends: higher quality (better), shorter delivery time (faster), and reduced cost (cheaper). The benefits described below illustrate how industrialized construction helps us reach those ends, and what organizations stand to gain by adopting it.
Improved Worker Safety and Career Longevity
Because work takes place in a controlled environment, industrialized construction minimizes many of the risks of traditional construction that currently impact worker safety — making things better for workers and enabling them to do better work for longer.
Industrialized construction promotes using industrial engineering techniques to design work cells that promote healthy ergonomics for the worker — with less bending, lifting, and climbing. The controlled environment of off-site work makes also makes it easier to implement workplace organization best practices (5S) and visual management so that the factory environment is safer and less cluttered for workers. Additionally, workers can more easily maintain and monitor tools and machinery for safety.
When the job moves on-site, industrialized construction makes work safer by reducing the number of workers, sequencing the work to reduce congestion, and reducing the materials stored and moved around the site.
Mistake-Proofed Projects and Products
Human error is inevitable. Understanding when and why humans make mistakes is the key to mistake-proofing and improving quality, and it’s another important aspect of how industrialized construction pushes us toward “better”: that is, better products and workflows. The manufacturing industry has worked to implement process and technology solutions designed to prevent mistakes that impact quality and create rework — such as inaccurate measurement, improper setup, wrong and missing parts, and operation errors — but many similar challenges and errors persist in construction.
Industrialized construction challenges owners and operators to mistake-proof work. These efforts start with design and engineering standards in the model and include automated bills of materials, work instructions, jigs and templates, and the use of sensors and other detection technology in the factory and the field. Work off-site in a factory environment makes it far easier to collect production data and gather insights from workers, diagnosing the root causes of defects and revealing where and how to intervene to mistake-proof processes.
Reduced Waste and Greener Buildings
The industrialized construction revolution also supports the construction industry’s increasing focus on decarbonizing buildings — a key aspect of what makes for better products. Many of industrialized construction’s aims — reducing materials waste, simplifying projects and components, and introducing methods that enable new, lower-intensity materials (such as mass timber) — also mean less embodied carbon in the built environment. In other words, industrialized construction can lead the industry to a more sustainable future.
Nearly one-third of building materials still end up in a dumpster. Manufacturing-informed designs create more accurate and reliable bills of materials far earlier in the process, which will continue to dramatically decrease the scrap rate across the industry.
Shorter Delivery Time
Data that we’ve collected working with general contractors and trade contractors reveals that the rate of productivity in fab shops is, at minimum, three times higher than in the field for companies that have reached manufacturing maturity.
This faster rate of production is compounded when teams can begin prepping for assembly in the field at the same time workers are fabricating assemblies and kitting components, and the concurrent operations allow the timeline to be significantly compressed. For example, a field team can pour a foundation and give it time to cure while, concurrently, factory workers assemble modular building components. Installation of those components can then happen in a matter of days.
Many industrialized construction approaches also lay the groundwork for teams and organizations to successfully implement automation, which, when done right, can support the move toward better, faster, and cheaper products.
Accelerated Learning and Innovation
Industrialized construction’s potential to make things faster also applies to worker learning and innovation. Centralizing work in a shop-floor environment, as opposed to spreading out production across geographically disconnected jobsites, can dramatically accelerate innovation in construction. The repeatability of the work and the ease by which we can use data and direct observation allows us to see problems and develop new prototypes and improvements more rapidly. And as mentioned above, continuous improvement and strong feedback provides a critical foundation for this rapid learning and improvement.
More traditional manufacturing in the United States has learned that the loss of manufacturing resulted in a slowdown in innovation and technology leadership. The construction industry can bring an unprecedented level of innovation to construction by bringing together off-site construction manufacturing methods, Lean product development approaches, and the current wave of technology investments in our industry.
Reduced Product Cost
It’s easy to see how “faster” leads to cost savings — higher productivity reduces labor time. But beyond labor efficiency in the shop, industrialized construction is proving to enhance productivity in the field by making assemblies easier to install. For example, approaching design in a way that considers how a product will be built and installed (vs. design for intent only) can eliminate unpredictability at the assembly stage, producing a better product more predictably and cheaply.
Kitting components and optimizing materials and deliveries on-site improves workflow and reduces waste, which makes it easier for the field team to execute the installation. We have measured the installed cost to be as much as 50% lower on projects utilizing industrialized construction methods.
Challenges of Industrialized Construction
For most of the design and construction industry, industrialized construction represents nothing short of transformation. And transformation comes with challenges:
Shifting mindsets
Industrialized construction may require changes in everything from leadership style to work processes to physical shop layout. People at every level of a company are likely to worry about how these changes will impact their jobs, and decision-makers will worry about budgeting for new technology, training, etc.
Knowing where to start
Haley & Aldrich’s construction manufacturing consultants have conducted scores of Industrialized Construction Maturity Assessments for companies and project teams, and one thing is almost always true: People think they’re farther along in adopting industrialized construction approaches than they really are. But knowing how to start your own transformation is impossible without a clear sense of your current state and concrete next steps to take.
Engaging partners
Many of the changes required to embrace industrialized construction require a deeper relationship with the supply chain and trade partners (e.g., moving from design for intent only to end-to-end product design, or launching new supply chain management software). Partners must be willing and able to engage for those shifts to work.
The Industrialized Construction Revolution
Industrialized construction is poised to take over the design and construction industry as teams discover how it can deliver more value on a more efficient timeline. It has already made strong inroads, particularly at organizations that already embrace Lean approaches.
Haley & Aldrich regularly assesses how effectively organizations and project teams utilize industrialized construction methods through its Industrialized Construction Maturity Assessment. The firm estimates that the industry as a whole is currently in an “early adopter” phase and is likely around 10 years from hugely transformative results.
Haley & Aldrich envisions a 50/70/70 future for construction: In the future state, the built environment will complete projects 50% faster, requiring 70% fewer jobsite deliveries and people, with 70% reduced carbon intensity.
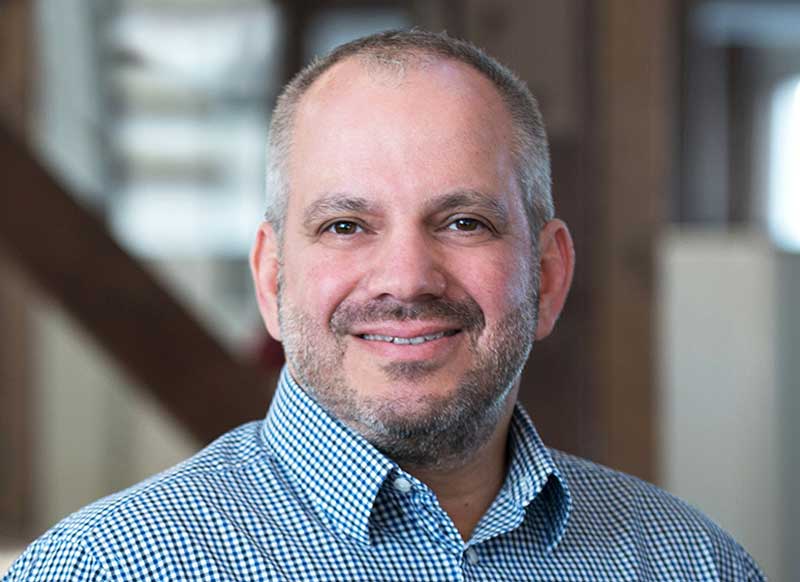
Nick Masci, Principal Consultant of Construction Manufacturing at Haley & Aldrich
“The term industrialized construction will ultimately vanish and just become construction, because at that point it will be the norm.”
Learn more about Haley & Aldrich’s construction manufacturing consulting services.
More Lean Topics
From 5s to IPD, explore popular Lean design and construction topics below.