Set-based Design
Introduction to Set-based Design
In the built environment, flexibility and adaptability are key attributes to possess while working on a project. This is more true the earlier you are in the project’s life cycle, where your processes and decisions can have a huge bearing on how much time your project will take and how much money it will cost.
Additionally, rework can be a huge obstacle for construction projects. Not only is rework frustrating and morale-crushing, it is also incredibly expensive and time-wasting. This is especially true in the design phase, as significant amount of rework early in the project can suck up costs that are needed for later on in the project and can lead to a lot of headache for all members of the team who are relying on the design phase to wrap up so they can advance the project forward.
For people in the design community, rework may seem inevitable. You complete a design only to find out that certain aspects of it don’t work together, and so you are asked to begin a totally new concept.
By utilizing a set-based design plan, you can give your team increased flexibility through the ability to explore a number of different design options early. This significantly reduces wasteful rework by adding that additional flexibility while also ensuring your project produces the best possible outcome.
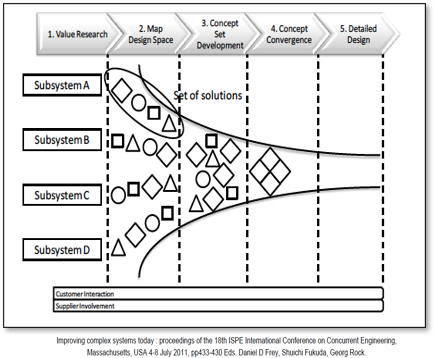
What is Set-based Design?
Set-based design, also known as set-based concurrent engineering, is a method that keeps requirements and options flexible for as long as it is responsible during the development process. This highly-collaborative process leads to less rework during the design phase.
Set-based Design in Practice
In traditional point-based design methodology, a design will be created and then tested before the team ultimately returns to the drawing board for rework when that design fails to meet a key requirement (often missing the mark on budgetary constraints).
In Target Value Delivery, we refer to this as the “value engineering loop,” where a product is designed, then developed without taking the budget into account prior to development. When utilizing a set-based design methodology, cost is used as an input of design instead of an output, significantly reducing rework in the process.
Through set-based design, the team also develops many different combinations of design options simultaneously to determine which of those combinations will yield the best outcome. These design options are all adopted and created concurrently, allowing for the most possible options until the last responsible moment.
While these designs are developed, the team considers the elements of each option and decides which designs to advance to the next stages based on agreed-upon criteria (such as the Conditions of Satisfaction). This process also creates flexibility for the team to pivot to a different option in case an issue arises with a certain element of one of the other options, or if the Conditions of Satisfaction change unexpectedly.
For example, let’s say you are working on a design for a building that could be built in one of three different places, using one of three different potential energy sources, and with one of three different flooring options. By developing designs for all of these nine potential combinations simultaneously and by eliminating options only at set decision points, you allow your team a tremendous amount of flexibility while reducing the odds that rework will be required on the design.
How to Implement Set-based Design
1. Main Player Onboarding
Strategically select a high-performing team of design and construction professionals to enlist in your project. Onboard your team to familiarize them with the goals of your project and the methodologies you will use. Foster trust and cohesion between team members and discuss strategies for communication and problem solving.
2. Strategy for Basing Decision in Value
What is the value proposition for this project? With your team, determine the desired outcome and work backwards from there. Alongside the CoS and cost indicators, the value proposition should drive all decision-making throughout the process. This includes decisions made centering around design options. Once you know the value proposition, you can accurately weigh the elements of each design option being considered during the design phase.
While it’s important everyone understands what should be driving decisions, that does not mean everyone must have the same ideas about what solutions to implement. Differing perspectives are welcomed in the built environment, if not required for driving progress.
3. Establish Conditions of Satisfaction
Representatives from project ownership, the design team, and the construction team must get together to determine the project’s Conditions of Satisfaction. Alongside the value proposition and cost indicators, the CoS will drive all decisions made throughout the project life cycle, including the design phase.
For the purposes of designing, you should not be developing a design if you already know that the design doesn’t fulfill elements of the Conditions of Satisfaction. Creating a design you already know won’t work is the definition of wasteful work.
4. Form Cluster Groups/Organize the Team
In order to accomplish a lot of work quickly – in this case, the completion of several different design concepts being developed simultaneously – split your team up into carefully-selected cluster groups. These cluster groups will complete their assigned work at the same time, speeding up the process.
5. IGEDIT
Once you have begun developing your different designs, follow the IDGEDIT process to determine which designs to advance and which designs to eliminate from contention.
Identify
The team first must identify various project elements, such as types of building skin (e.g., curtain wall, EIFS, tilt-up precast), and assess them in relation to the project definition and targets. These elements constitute the design sets in set-based design, and the team will progressively narrow these down to select the most optimal solution over time.
Gather
Once options have been developed and a tracking method and format have been agreed upon (like an A3 document), the project team collects the necessary information to thoroughly evaluate each option. While the specific value-based decision tool deployed typically determines the required information, the essential objective elements include scope definition, affected systems, and variations in options, along with conceptual cost and schedule implications.
In addition to objective data, subjective information is vital for making a final decision based on value. This may encompass factors such as aesthetic appearance, complexity of maintenance, employee satisfaction, and other qualitative considerations.
Evaluate
Next, the team evaluates the various options according to the Conditions of Satisfaction and other important factors and targets. Outline the elements of each option from an objective lens, and listen to all perspectives on these options.
In order to ensure maximum flexibility and to keep options open while elements of the project are still in flux, decision-making should be postponed to the last responsible moment as dictated by the project Milestone Plan.
Depending on the complexity of the evaluation, the team can navigate this process using various tools, such as Choosing by Advantages, cost/benefit analysis with payback, and stakeholder presentations and feedback.
The team should prioritize option evaluations based on the perceived difficulty of reaching a decision. For example, some decisions may seem straightforward, with one option clearly meeting all the value criteria and positively impacting project cost and schedule targets. Meanwhile, other options may demand extensive evaluation and substantial discussion. Apply thorough scrutiny where necessary to avoid spending valuable time assessing options that are obvious and require minimal deliberation.
Decide
Once the team has weighed all of the available design options, come to a decision on which design to advance to the next phase of the project, which will likely require a more detailed design.
As you are advancing options to the next phase, take note of which options are mutually exclusive from one another. For instance, a decision to go with a curtain wall system would exclude or reduce the options available for a future evaluation of window/glazing types applicable to other skin systems.
Implement
The decision on the chosen option marks the point at which designers can proceed with refining the design details (production design) for the project. As the team aims to minimize effort until decisions are finalized, this step empowers designers to focus on the production and coordination of the design model incorporating the selected option.
Throughout the development of drawings, estimators maintain communication with designers to track the progress of option design and confirm initial assumptions as the detailed design work advances.
Test
Once the option design details reach a sufficient level of development, the estimating team employs a production-estimating methodology to validate the initial objective assumptions and conceptual costs used during the evaluation stage.
It’s important to also verify the subjective factors of the option against the original evaluation. In the event of any discrepancies in cost, schedule, or value factors in the final state of the option, these must be updated on the value-tracking and value-decision forms. This ensures that subsequent decisions are based on the most up-to-date information.
The team also conducts a review of variances as feedback to the evaluation and decision-making steps, in the spirit of the “adjust” phase of PDCA. This step aims to identify any necessary changes to the process or conceptual cost estimating inputs that will lead to more accurate evaluations in the future.
Learn Set-based Design
The Lean Construction Institute is committed to transforming the design and construction industry by providing Lean educational resources, conducting field research, and facilitating local and national Lean events. Explore the supplementary resources below to further your understanding of The Last Planner System.
Lean Assessments
How strong is your Lean knowledge? Take a Lean assessment to determine your current state so you have a baseline for improvement. Lean assessments are available for individuals, teams, and organizations alike. Whether you’re new to Lean or are an experienced Lean practitioner, Lean assessments are a great way to get started at LCI!
TAKE ASSESSMENTMore Lean Topics
From 5s to IPD, explore popular Lean design and construction topics below.